This customer showcases blog highlights Taggares Fruit Company’s adoption of Croptracker’s Harvest: Pre-Print and Scan. Taggares is headed into their second season recording their harvest inventory with Croptracker and we spoke with Taggares’ Systems Manager, Logan Janin about the benefits they have already gained from their first year of Croptracker.
Taggares Fruit Company has a long history in Washington State. Pete Taggares I started the original family farm in Prosser Washington shortly after immigrating. This farm is still owned and operated by the family today. Pete Taggares II scaled up the farm business into Othello in the 1950’s with 3000 acres of potatoes. Pete II grew the company with potato processing plants and founded the Chef Reddy brand. Pete II also expanded into Apple and Grape farming with a large orchard and vineyard in the Snake River Valley. The Taggares brand included fresh fruit and jam, at one time becoming “the largest Concord grape vineyard in the world”.
Today family involvement with Taggares continues as Pete Taggares III and Pete Taggares IV are still involved in operations at Snake River Orchard. Pete III retired from overseeing farm operations in 2014 but still consults in the business. Pete IV is the current CEO of Taggares Fruit Company. Snake River Orchards now continue to grow high-value apple varieties and concord grapes.
Taggares initially approached Croptracker to help them improve their harvest tracking system. Like many growing and packing operations, Taggares has many different software solutions to track their operations and expenses. Adopting new solutions is often painful due to disparate information organization systems and a lack of integration between systems. Croptracker’s software is modular so replacing parts of an operation and making changes without disrupting other processes is easy. Croptracker reports and data are exportable in multiple formats meaning linking data into existing systems is possible.
Croptracker has saved us hours and hours of just comparing things because now we have the data on the go rather than just literally hand counting the tickets at the end of the day. And again, we did 2000 bins yesterday so it used to take hours.
As a systems manager, Logan is well-versed in the challenges of integrating new workflows and software. Logan needed to make sure moving their harvest tracking to Croptracker was not disruptive. Taggares uses Picktrace for labor tracking among several other farm management software systems and pulls all information together into Power BI. Croptracker worked with Logan to integrate data with Picktrace seamlessly.
Taggares Harvest workflow involves pre-printing bin tags to create and track inventory throughout the rest of their processes including linking with picker information from Picktrace. Before harvest starts for the day, bin tags for the areas being harvested are printed out. Croptracker support staff worked with Taggares to create a custom tag format to suit their needs. The tag includes a barcode format that can be read by PickTrace software. This code links picker information to the individual bin they harvested, removing the chance for manual data entry errors.
The bin tag Taggares uses is split into three parts. The top two parts contain the same information. One part will go to the picker so they can track their bin totals to make sure they align with the pay information from Picktrace. The second part of the tag will go with the QC team so they can line up their sample results with the inventory they came from confidently. The third part of the tag is affixed to the bin itself and will follow the bin through storage and packing for traceability. All information about the inventory, picker data, QC data, and storage location information, is aligned by Logan in Power BI using the Croptracker-generated codes.
Once the tag is on the bin and the additional information has been confirmed, the tag is scanned in the field using the Croptracker offline harvest app and becomes a digital inventory record. As information is synced throughout the day, staff in the warehouse can see harvest totals and plan for incoming inventory. This digital record is an important part of Taggares' overall traceability system and provides accurate harvest yield records on the go.
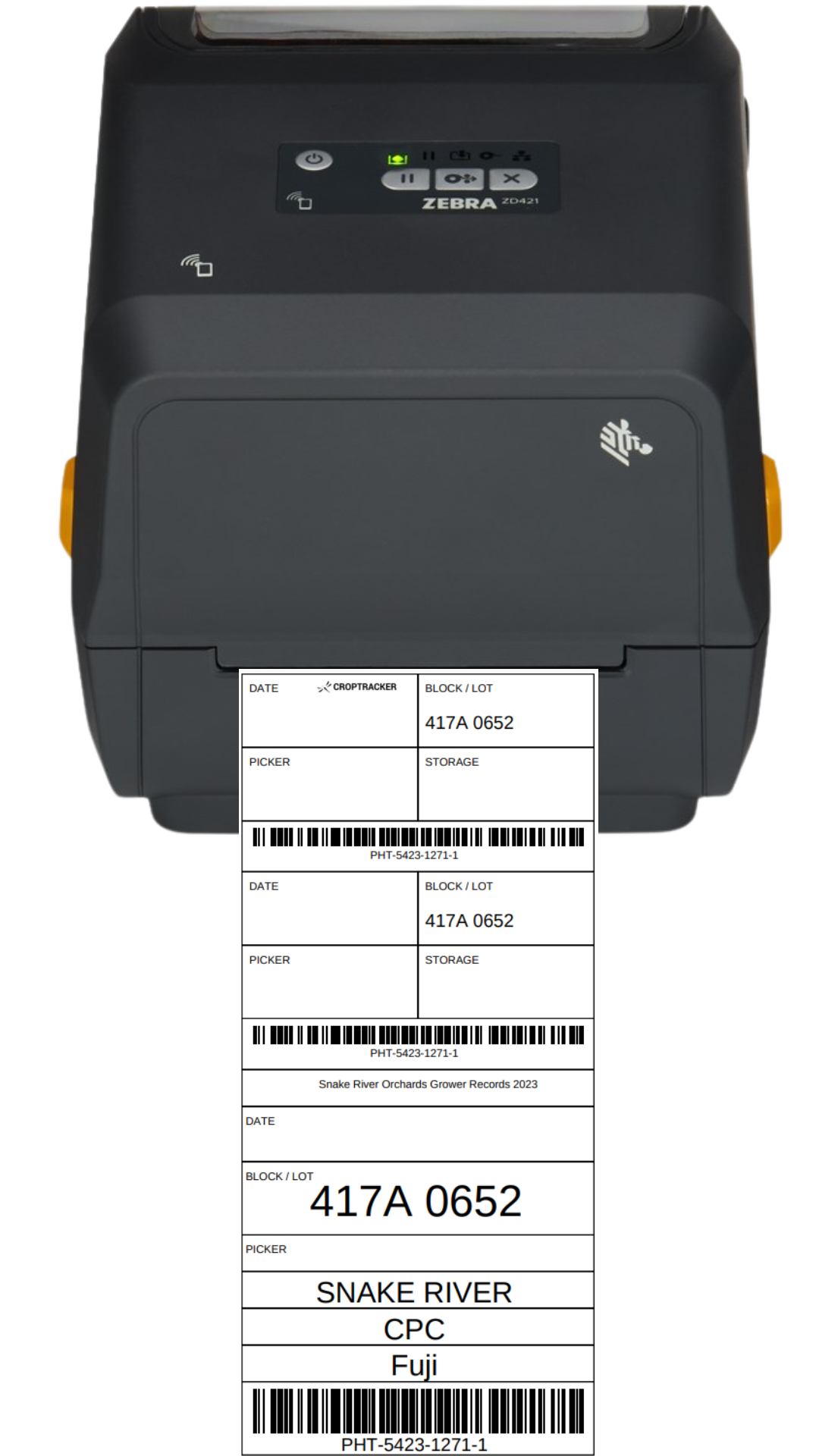
Previously, Taggares had a complicated bin ticket printing system, not specifically designed for agriculture. Only a few staff were able to successfully operate this system. Logan was consistently called in during off hours to help troubleshoot and tag print. At the end of every harvest day, several staff members would also have to spend hours correcting errors and aligning information from pickers, quality control, storage and pack house teams.
Croptracker has saved us hours and hours of just comparing things because now we have the data on the go rather than just literally hand counting the tickets at the end of the day. And again, we did 2000 bins yesterday so it used to take hours.
Taggares Fruit Company's integration of Croptracker's Harvest: Pre-Print and Scan workflow underscores their commitment to efficient, accurate, and integrated harvest tracking. With a rich legacy spanning generations and diverse agricultural ventures, Taggares recognizes the value of modern solutions in streamlining operations while maintaining quality and reliability. Logan Janin's testimonial reflects the tangible benefits of Croptracker, saving crucial hours daily by seamlessly linking harvest data with labor tracking systems and enabling real-time inventory visibility. This approach not only minimizes manual errors but also enhances traceability across the supply chain, from picker to QC to storage and beyond. As Taggares embarks on their second season with Croptracker, their ongoing success exemplifies the transformative impact of tailored agtech solutions in today's dynamic farming landscape.